
5-Axis Simultaneous Machining
SolidCAM's mature and powerful five-axis simultaneous machining technology
- 01
Flexibility and controlforce
- 02
Collision Avoidance for Tool and Gripper
- 03
Edge Trimming and Edge Trimming
5-Axis Simultaneous Machining
Benefit from the most extensively tested and validated five-axis machining toolpaths in the industry, featuring a user-friendly interface, collision detection, and state-of-the-art control over all aspects of the toolpaths:
-
Extensive 5-axis simultaneous cutting strategies
-
Streamlined cutting generates toolpaths that follow the natural shape of the part
-
Multi-sided mirror machining keeps the tool perpendicular to the surface (or at specified lead and tilt angles), providing a smooth surface quality
-
Advanced tool tilt control, directly managing lateral tilt and lead angles
-
Automatic collision avoidance strategy, checking every part of the tool and fixture
-
Multi-axis rest roughing efficiently removes remaining material from previous larger tool diameters
-
Realistic full 3D machine simulation, including comprehensive collision and axis limit checks.

Flexibility and Control
Each 5-axis machining strategy offers precise entry/link control and tool axis control options.
The link and entry movements are equipped with collision avoidance features, and different strategies can be used based on the distance of the link movement. SolidCAM also provides control options for the lead and tilt angles, allowing complete control over the final toolpath.
Collision avoidance for tool and holder
The collision avoidance feature supports tools and fixtures, providing a range of strategies to prevent collisions. Machine simulation offers a complete visualization of the protrusion check.


Automatic Edge Trimming
After machining CAM parts, it is sometimes discovered that there are burrs along straight edges or non-tangent exterior surfaces. These are formed when the tool removes metal from the edges and can compromise the functionality of the part or pose a safety risk due to their sharpness. Therefore, removing them is the best option.
SolidCAM's Edge Trimming operation creates a deburring toolpath along the outer edges of the part's geometry. The tool's position relative to the edge is always bivector between the two surfaces of that edge.
-
By selecting only the part's geometric shape, a fully automatic toolpath can be created.
-
Other features include automatic feature detection, linking, lead-in, and collision avoidance.
-
To run the detection feature correctly, a ball end mill and well-defined geometric inputs are required.
Automatic Edge Trimming
SolidCAM's edge trimming operation efficiently processes parts that require edge trimming to achieve the final shape. This operation utilizes highly automated algorithms to generate tool paths for trimming thin materials.
-
Designed specifically for edge trimming thin materials.
-
The position of the tool relative to the geometric shape can be defined through various options, ranging from 3-axis output to more complex 5-axis output, with different tool axis orientation choices.
-
Axial displacement allows the tool to make certain contact with the material.
-
Edge trimming can be automated or customized by the user, offering various corner handling capabilities to create smooth tool paths.


Special 5-Axis Machining Strategies and Functions
Chip Processing

In chip machining, the tool is tilted to utilize its side surface for cutting. Chip cutting takes advantage of the full cutting length of the tool, resulting in better surface quality and shorter processing time.
Multi-Blade Machining

The multi-blade machining operation can easily handle parts such as impellers and blade discs, widely used in various operations. It offers multiple strategies for efficiently roughing and finishing each part of these complex shapes.
Through hole processing

Through 5-axis machining operations, you can use tapered cylindrical tools to process intake and exhaust pipes, inlet and outlet ports of pumps, and passages within steel blocks. You can quickly and easily define roughing and finishing operations while maintaining complete control over the entire tool and tool holder collisions through reliable simulations.
Contour 5-axis Machining

The 5-axis contour machining strategy tilts the tool along the linked 3D contour-driven curves while aligning the tool axis according to the defined tilt lines. This machining strategy is highly suitable for generating 5-axis tool paths used for deburring and trimming purposes.
Multi-Axis Drilling

The multi-axis drilling operation utilizes SolidCAM's automatic hole recognition feature to perform drilling, tapping, or drilling cycles swiftly and easily in any hole orientation. This operation provides all advanced linking, tilting, and collision avoidance strategies.
Convert HSM to 5-axis simultaneous machining

Converting HSM 3D toolpaths into complete 5-axis collision-protected toolpaths. This will maintain the optimal contact point between the tool and the part and allow the use of shorter tools for improved stability and rigidity.
Rotary Processing
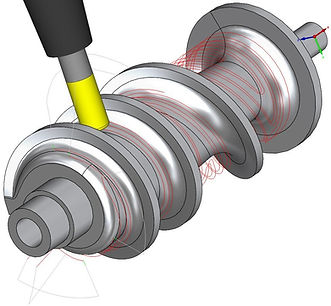
Using cylindrical, ball-end, or flat-end tools to generate 4-axis rotational roughing and finishing toolpaths for screws.